- 10 June 2024
- by Andrej Fedek
- Blog, Business, Resources & Tips
- 0 Comments
Running busy store locations stocking many shelves with different important cooking ingredients or build crews on big construction sites keeping truckloads of building materials on hand gets tricky managing what remains available daily vs delivered out/used up during extreme workload periods. But convenient self storage facilities nearby offer expandable rooms securely tracking inventories efficiently. For example, detailed computer lists seeing boxed supplies scanned entering/leaving portable storage warehouses lets managers easily restock items faster maximizing workflow continuousness shipping replacement inventory parts reducing “out of stock” slowdowns losing customers ultimately. Let’s review clever inventory management techniques maximizing operational efficiencies using self-storage capacities!
Categorize Items Similarly
Some families/businesses waste hours digging through messy storage bins trying finding important things urgently. Professional organizer Brianna Murphy knows neatly labeled clear plastic totes sorted keeping similar items together at facilities like self storage units saves hassles rummaging disorganized jumbles.
For example, pack spare workout clothes separately from old kids’ toys stored preserving childhood memories without chaos jumbled cluttering special pieces unnecessarily when simple categories help. Signs listing box contents also prevents reopening containers checking each one to remember where specific things remain stored conveniently between uses rather than unpacking everything frustratingly rediscovering needed items yearly.
Note: Historical palace archives reveal Egyptian society sophisticated categorical information storage systems hierarchical labeling organizes governing administration clay tablets circa 3000 BCE!
Monitor Inventory Levels Responsibly
Managing what remains stored offsite optimizes workflows by:
- Counting items entering/exiting noting running totals proactively
- Scheduling routine inventory recheck dates before depleting unexpectedly
- Tracking usage rates calculating ideal restocking orders responsibly
- Photographing storage box contents limiting frequent visual verifications
- Investing minimal technology like barcode labels improving accuracy immensely
The Small Business Administration provides inventory management education. Expert Neil Wallace reminds “data visibility identifies insights – quantify operations maximizing personal oversight limits otherwise.” Information fuels intelligent choices!
Rotate Stock Keeping Things Fresh
Letting excess food ingredients wait untouched for long periods seems wasteful if groceries expire sitting forgotten far back storage closets undiscovered when initially craving certain recipes suddenly. Expert chef Jordan Murphy knows “responsible kitchen managers intentionally order sensibly aligned actual customer demands weekly rather than blindly overpacking shelves driving unnecessary spoilage uphill battles trying keeping everything persevered maximally with limited budgets.”
Her guidance rotates fresh ingredients forward systematically while freezing perishable overflow surplus minimally allowing flexibility adjusting dishes if seasonal tastes fluctuate unexpectedly week to week. Research studies confirm proactively planning logical material rotations eliminating food waste rather than reacting last minute trying salvaging soon inedible leftovers scrambling unreasonably through final service hours nightly. Streamline mindfully what customers crave timely.
Meet Changing Space Needs
As business product orders fluctuate seasonal when holiday gifts ship each winter or summer yard decor expands selling faster than makers produce currently, extra storage helps companies handle needs flexible by:
- Keeping enough safe overflow space securing urgent stockpiles as required
- Moving items efficiently between varying unit sizes rented monthly
- Eliminating long warehouse leases wasting money for unused square footage minimally
- Protecting unfinished works progress within dust-free spaces speeding transportation as finished goods ship quicker using professional movers in Miami assisting freight logistics reaching retailers responsively meeting public purchase demands more fluidly ultimately.
Strategic expandable spaces prevent profits pinching unnecessarily through intelligently scalable solutions reacting promptly as market conditions signal responsively beyond sole internal capacities reacting otherwise.
Track Detailed Locations Digitally
Special electronic barcode tags stick items automatically logging computers exactly pinpointing stored gear locations down exact shelves rented explains industry technology expert Neil Simmons. He knows new tracking abilities lets warehouse managers see virtually what fills rooms digitally avoiding previous hassles trying updating giant paper floorplan maps by hand inefficiently redrawn each month remembering correctly where over 3000+ containers stack among units floor to ceiling through enormous commercial facilities realistically otherwise before futuristic improvements emerged.
Some self storage systems even scan driver licenses logging access automatically preventing mistakes identifying friends visiting tenants legitimately if questions arise later investigations valuable item misplacements unexpectedly. Check what business tech sites say smart inventory control – get ready as technologies expand change expectations even smaller family storage usage leveraging conveniences benefiting users enjoyably regarding unit contents oversight details!
Stat Box:
- 93% of large warehouses use tracking technology now
- 76% of small businesses want easy inventory apps
Automate the details seamlessly!
Simplify Inventory Management Strategically
Using neat categorization systems, closely monitoring stock usage levels, rotating surplus sensibly and adopting simple helpful technologies prevents inventory limiting business operations profitably over time through conveniently scalable self storage capacities managing overflows pragmatically as market conditions vary unpredictably. Set yourself success implementing fundamental data visibility and planning tools reaping benefits from smooth workflows sustained dependably despite fluctuations disrupting competitors lacking resilient supply chain infrastructures uniquely offering strategic assurances safeguarding customer commitments through stormy conditions responsively.
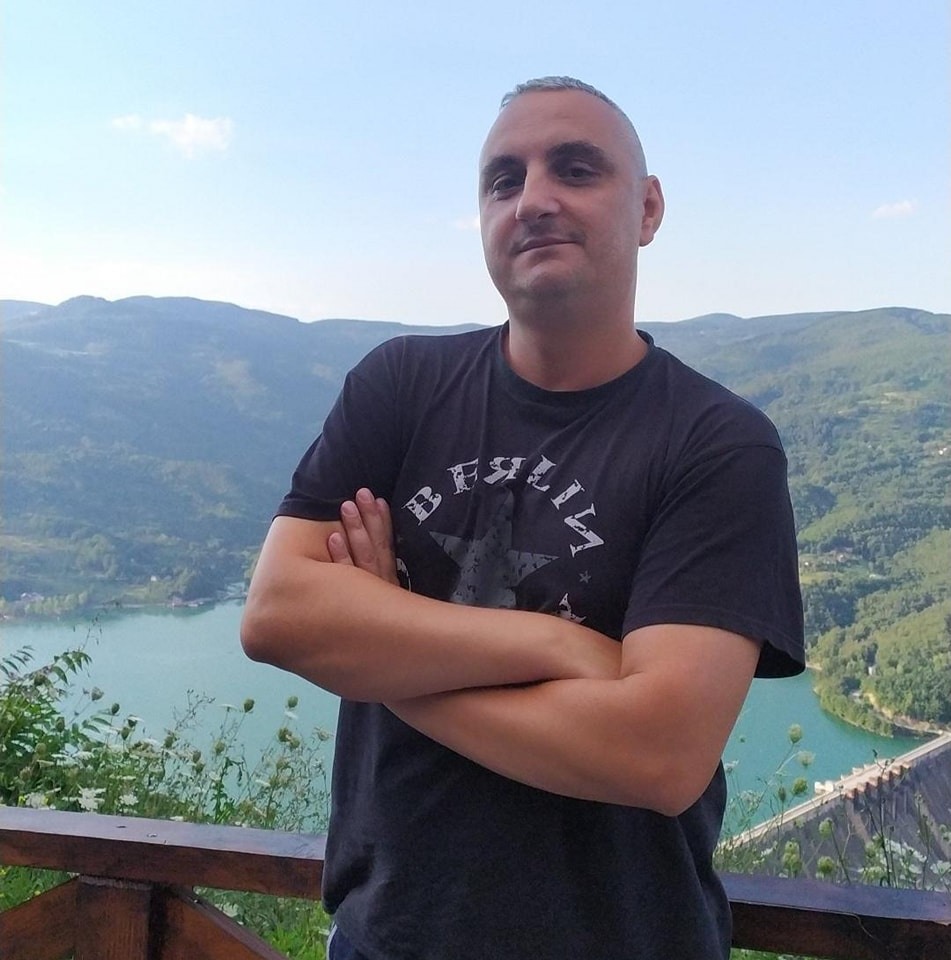
Andrej Fedek is the creator and the one-person owner of two blogs: InterCool Studio and HarmonyStart. As an experienced marketer, he is driven by turning leads into customers with White Hat SEO techniques. Besides being a boss, he is a real team player with a great sense of equality.